在现代制造业中,选择合适的刀具材质对于提高生产效率和降低生产成本至关重要。特别是对于铝合金材料的加工,由于其特殊的物理化学特性,刀具的耐用性成为影响加工质量和效率的关键因素之一。本文将详细介绍硬质合金刀片的材质性能如何选择,以及铝合金铣刀耐用性的影响因素,并探讨如何通过定制服务来满足特定加工需求。
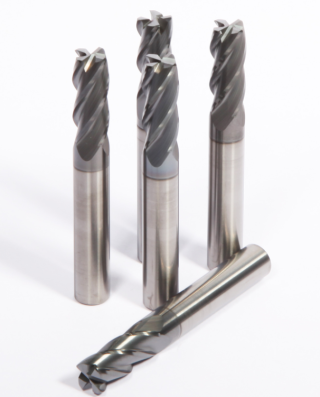
硬质合金是由碳化钨(WC)粉末与钴(Co)或其他金属粘结剂混合而成,具有极高的硬度和耐磨性。在选择硬质合金刀片时,需要考虑以下几个关键因素:
碳化钨含量:碳化钨是硬质合金的主要组成部分,提供了刀具的高硬度和耐磨性。一般来说,碳化钨含量越高,刀具的硬度和耐磨性越好,但韧性会相应降低。因此,在选择时需要根据具体的加工条件进行权衡。
钴含量:钴作为粘结剂,能够提高硬质合金的韧性,使其在承受冲击载荷时不易断裂。高钴含量的硬质合金更适合断续切削,而低钴含量则适用于连续切削。
粒度大小:硬质合金的粒度大小直接影响到刀具的锋利度和表面光洁度。细粒度的硬质合金刀具具有更好的切削性能和表面质量,但成本较高;粗粒度的硬质合金刀具则更经济实惠,但切削性能略逊一筹。
涂层类型:为了进一步提高硬质合金刀具的耐用性和性能,通常会在其表面涂覆一层或多层耐磨材料,如氮化钛(TiN)、氮化铝钛(AlTiN)等。不同的涂层材料具有不同的特点,例如TiN涂层具有良好的耐磨性和较低的摩擦系数,而AlTiN涂层则具有更高的耐热性和抗氧化性。
铝合金材料的加工难度较大,主要是因为其具有较高的热导率和较低的熔点,容易导致刀具过热和磨损。以下是影响铝合金铣刀耐用性的几个主要因素:
切削速度:过高的切削速度会导致刀具温度升高,加剧磨损。因此,需要根据刀具材质和工件材料选择合适的切削速度。
进给量:适当的进给量可以减少刀具与工件之间的摩擦,降低磨损。过小的进给量会导致刀具与工件长时间接触,增加磨损;过大的进给量则可能导致切屑堵塞,影响加工质量。
切深:切深过大会增加刀具的负荷,导致磨损加剧。因此,需要根据刀具材质和工件材料选择合适的切深。
冷却液:使用合适的冷却液可以有效降低刀具温度,减少磨损。常用的冷却液有水溶性冷却液和油基冷却液两种,具体选择取决于加工条件和工件材料。
刀具几何形状:合理的刀具几何形状可以减少切削力,降低磨损。例如,采用较大的前角和后角可以提高切削效率,减少磨损。
刀具涂层:如前所述,刀具表面的涂层可以显著提高其耐用性和性能。选择合适的涂层材料和厚度对于延长刀具寿命至关重要。
对于有定制铣刀需求的客户来说,选择一个专业的刀具厂家非常重要。如厂家资质,选择具有相关行业认证和资质的厂家,如ISO 9001质量管理体系认证等。与厂家详细沟通自己的加工需求和技术要求,确保厂家能够准确理解并提供满意的解决方案。选择提供完善售后服务的厂家,以便在使用过程中遇到问题时能够得到及时的支持和帮助。
总之,选择合适的硬质合金刀片材质和优化铝合金铣刀的设计对于提高刀具耐用性和加工效率至关重要。通过与专业的刀具厂家合作,如:龙星刀具厂家,客户可以获得定制化的解决方案,满足特定的加工需求。无论是标准产品还是特殊应用,专业的刀具厂家都能够提供高质量的产品和服务,帮助客户实现高效、精确的加工目标。